Marantz SD9000/SD8000 Compudeck Optical Sensor Repair
Overview
Initially offered in 1980 as the flagship of the Marantz
cassette deck line, the SD9000 Compudeck was one of the best-built, most
feature-packed cassette decks ever offered for consumer use. Retailing at
$900.00, the SD9000 utilized two DC servo motors for precision tape control and
three heads for direct tape-to-source comparison as you recorded. Way
ahead of its time, the SD9000 also incorporated an advanced
microprocessor-controlled music search feature, allowing you to program which
songs on a given cassette you wanted to listen to, as well as the order in which
you wanted to hear them. The SD9000 also offered a digital function for
automatic timer recording or playback - accurate to the minute. In
addition, the SD9000 included a slew of other advanced features like bias fine
adjustment, an auto tape slack removal circuit, mic/line mixing, electronic
timer memory, solenoid-controlled feather-touch full logic transport, and the
list went on. The Marantz SD8000, a slightly more economic choice, shared
virtually all the features of the SD9000, however in a two-head design.
A Fatal Flaw?
Unfortunately, over the years, the SD9000 and its little
brother, the SD8000 proved to have an "Achilles Heel". Both decks used a
pair of optical sensors to generate the reel turn count pulses for their
on-board microprocessors. This microprocessor also interpreted lack
of these pulses as a signal that the end of the cassette had been reached, and
would send an "all-stop" command to the transport 1.5 seconds after pulse
cessation. After ten years or so, depending upon use, these optical
sensors (also known as 'optocouplers') would weaken and fail. The symptom?
After one or two seconds in any mode, Play, Rewind, or Fast Forward,
the deck simply returns to the Stop mode. Over the course of 30+ years,
the failure percentage of these optocouplers approaches 100%. Worse than
the almost certain failure of these key components is the fact that the
original replacement optocouplers are no longer available, rendering these
expensive cassette decks essentially useless.
Fortunately, these decks can be brought back to life with
commonly available substitute parts, an hour or two of work, and a little
patience. Here's how:
Tools/Supplies You'll Need:
-
Soldering iron - a smaller 15-20 watt iron is ideal
-
Solder - "60/40" or "63/37" rosin core is the stuff you
want (never use acid core solder for electronics!)
-
Solder wick - get this at Radio Shack or your local
electronics supplier
-
90% isopropyl (rubbing) alcohol
-
Q-Tips - about a dozen or so
-
#1 and #2 Phillips screwdrivers
-
Small #1 or jeweler's flat-head screwdriver
-
"T10" Torx screwdriver or 2.5mm hex key (Allen) wrench,
or
3/32" hex key wrench - any of these will work
-
Small wire cutters (I use an old toenail clipper!)
-
Long-nose pliers
-
Regular pliers or small crescent wrench
Parts You'll Need:
Optek makes an optocoupler with suitable
specifications in all criteria for this application except for physical
size - it's too large (full manufacturer's data sheet is
here).
We'll need to modify it as will be seen later. Go to
www.mouser.com, and in the "Part# /
Keyword" search box, enter the following part number: 828-OPB818, or
click
here. Order at least two; at approximately $3.00 each, I'd
order a few extra for spares, just in case you damage one during the
modification. Mouser has no minimum purchase, and the USPS
Priority Mail shipping option they offer will get you these parts
quickly and cheaply.
By the way - it probably isn't a bad idea to order
replacement belt and idler tire kits for your deck while you're waiting
for your optocouplers, since you'll be deep into your tape transport
anyway. I've ordered several sets from Bob Toepfer at
Vintage
Electronics with excellent results. As of this writing, current price
for the belt kit is $15.00 and $30.00 for the idler tire kit. Not
exactly cheap, but I believe these decks are certainly worth the
investment.
The Fix:
Step 1
Okay, let's get down to it! Start by removing the top three case
screws with your #2 Phillips, as shown: |
|
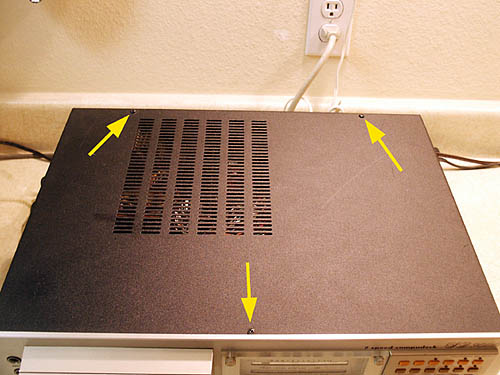 |
|
|
|
Step 2
Next, remove the two case screws on each side: |
|
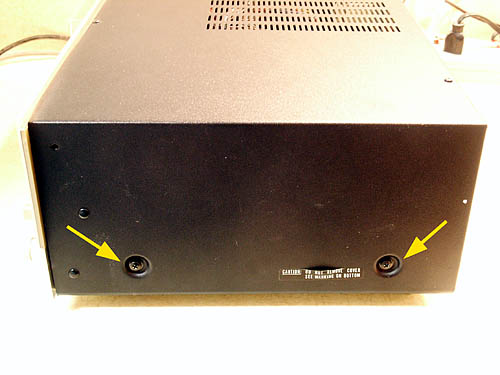 |
|
|
|
Step 3
Remove the outer metal case and set it aside. Remove the
hinging plastic tape head shield (if you're lucky enough to
still have one). Remove the knurled finger screws from the
front panel (see yellow arrows). These screws secure the
top metal "Marantz" panel and the lower clear plastic head
adjustment cover - remove them and set them aside. |
|
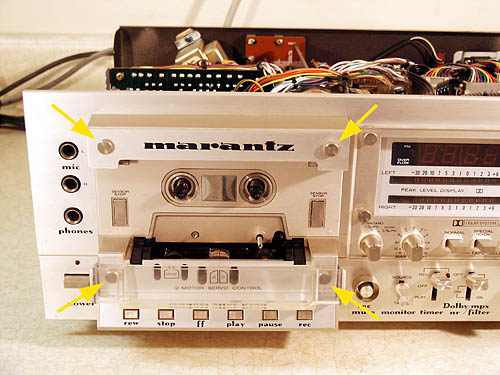 |
|
|
|
Step 4
Remove the two recessed Torx screws holding the plastic
cassette housing assembly in place (see arrows). |
|
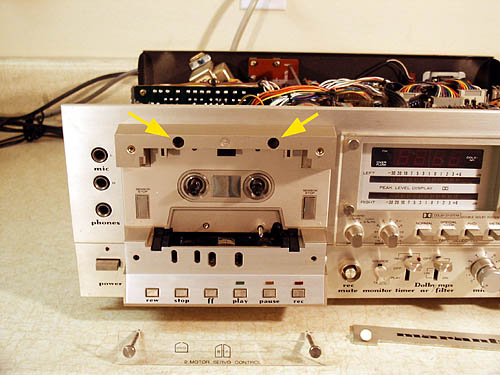 |
|
|
|
If you don't have a T10 Torx screwdriver handy, a 2.5mm metric
hex key wrench will work. If you only have English hex key
wrenches, a 3/32" will be a bit loose, but should still work. |
|
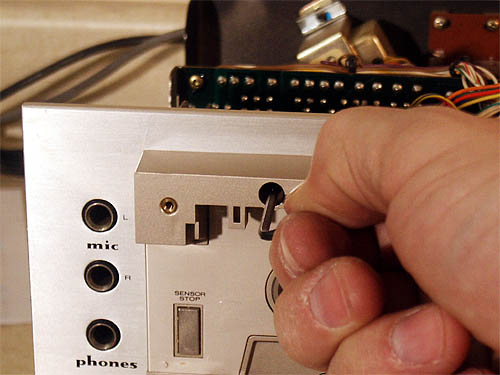 |
|
|
|
Step 5
Tilt the cassette housing forward (catch the Torx screws you
just loosened as they fall out), and set the assembly flat, as
shown. |
|
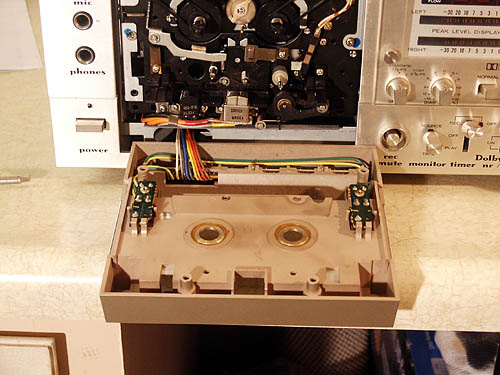 |
|
|
|
Step 6
Locate plug P508 on the main control board as shown, and unplug
it. This is the connector for the cassette housing switch
panel you just removed in step 6. |
|
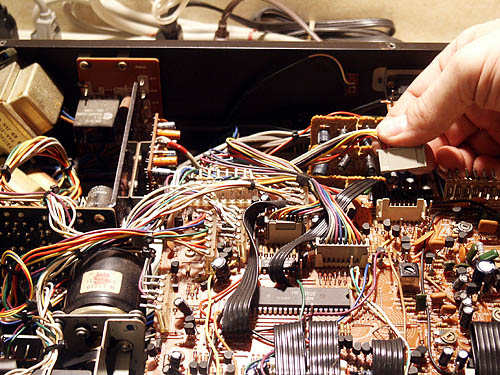 |
|
|
|
Step 7
Thread the P508 connector down through the other wiring while
gently pulling on the cassette housing, as shown. You may
need to cut some wire ties to do this. Fish the connector
through the opening below the cassette transport mechanism and
set the entire plastic cassette housing aside. |
|
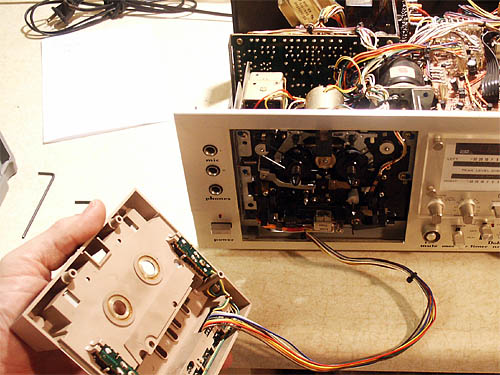 |
|
|
|
Step 8
Remove the two cassette transport assembly securing screws, as
shown. |
|
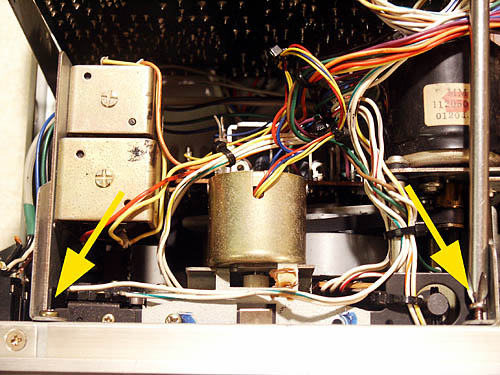 |
|
|
|
Step 9
Flip the deck over and remove the four remaining screws holding
the tape transport in place, as shown. |
|
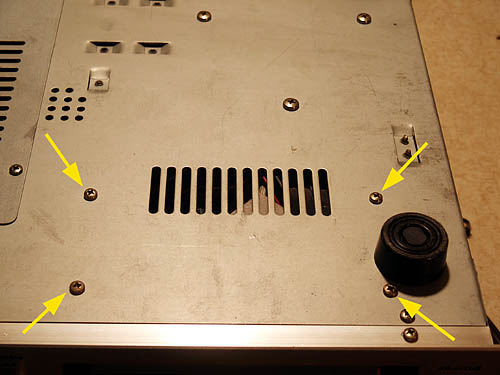 |
|
|
|
Step 10
Turn the deck right-side-up again, and locate plug P503, as
shown. Remove it gently. Always grasp the plug body,
not the wires, when pulling. |
|
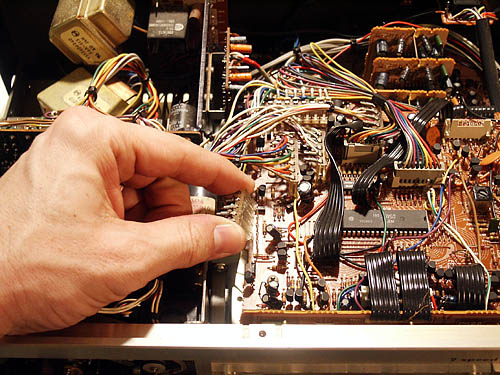 |
|
|
|
Step 11
It's a really good idea to mark the connector designations on
the
connectors themselves, since it is
possible to plug a connector
into the wrong receptacle on this model! |
|
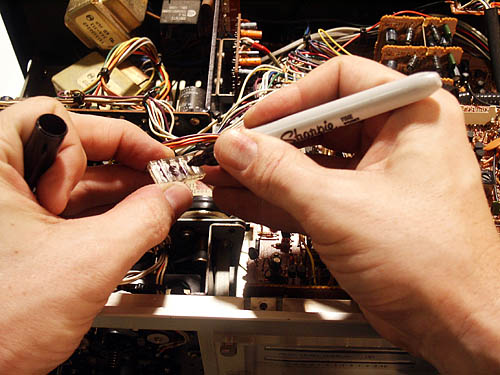 |
|
|
|
Step 12
Remove and mark connector P502. |
|
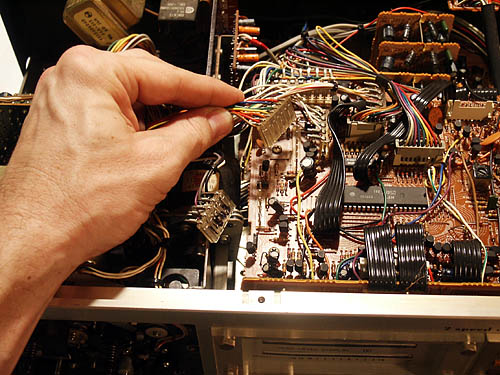 |
|
|
|
Step 13
Next, remove and mark connector P501. |
|
 |
|
|
|
Step 14
The last connector, P206, is located on the lower board, below
the microprocessor board. Resist the temptation to just yank on the
wires, and use your long-nose pliers to disconnect it. |
|
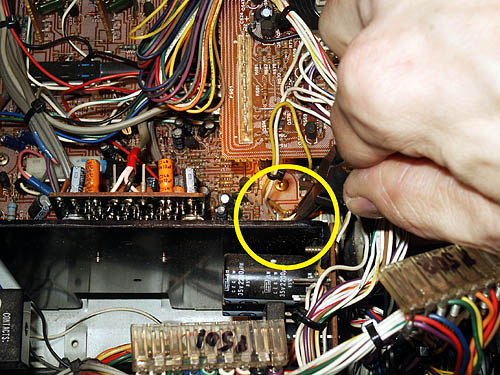 |
|
|
|
Step 15
To give yourself enough room to maneuver the tape transport out
of the deck where you can work on it, you'll need to remove the
four Phillips-head screws holding the power supply board in place.
The first two are shown here. |
|
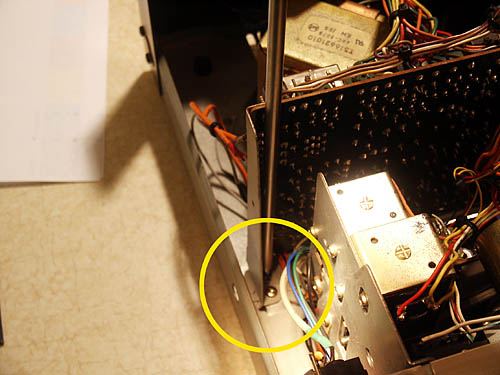 |
|
|
|
Step 16
Remove the third power supply board screw, located between the power supply board and the microprocessor board. |
|
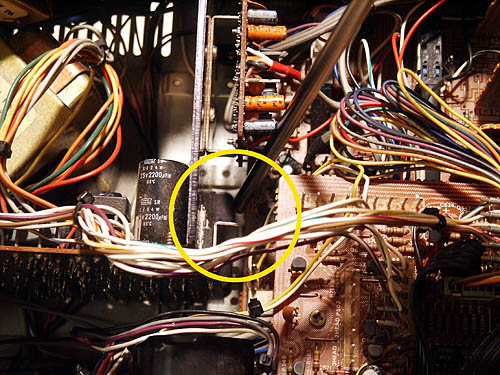 |
|
|
|
Step 17
Remove the last power supply board screw, located towards the
rear of the deck, between the power supply board and the
microprocessor board. |
|
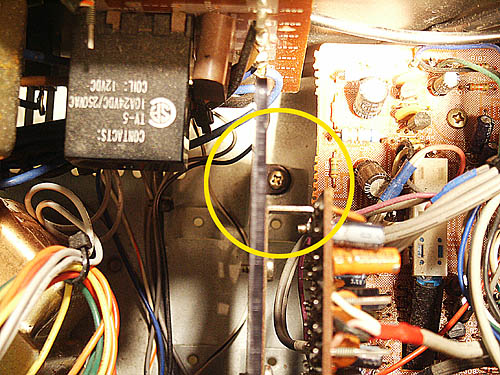 |
|
|
|
Step 18
Gently move the tape transport assembly towards the back of the
deck, then up and out, so that the reel hubs clear the opening
in the deck's front panel. |
|
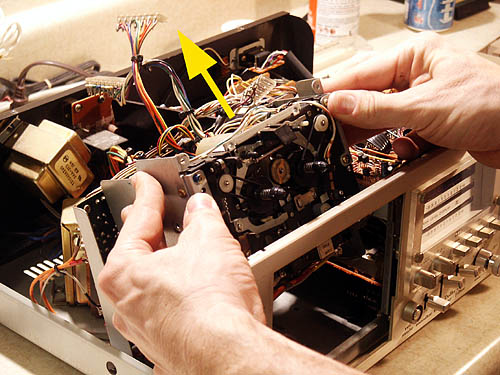 |
|
|
|
Step 19
Lift the transport clear of the chassis and place it on a towel
to prevent it from being scratched. The signal wires from the
record/play/erase heads will still be connected; be careful not
to place stress on them as you maneuver the transport. Remove the Phillips screw securing the motor driver board to the
transport housing. |
|
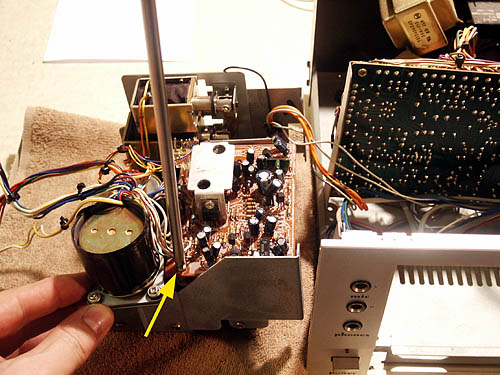 |
|
|
|
Step 20
Tilt the motor driver board up and pull it towards you (as in
the picture) to remove it from the slotted retaining clip on the
far side of the board. |
|
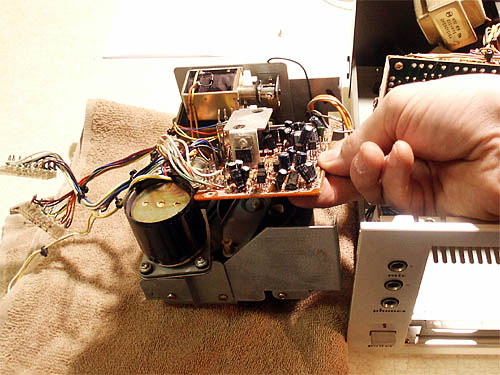 |
|
|
|
Step 21
Remove the Phillips screw securing the motor driver board
retaining clip, and then remove the clip. Use a standard pliers to
remove the brass threaded hex bushing (lower arrow), and
remove the flywheel retaining bar. |
|
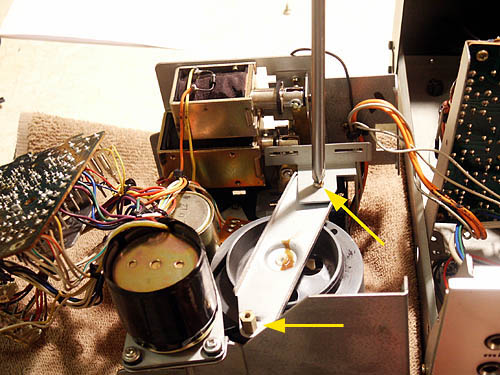 |
|
|
|
Step 22
Remove the flywheel drive belt with a pair of long-nose pliers
that has been cleaned with a rag dipped in 90% rubbing
(isopropyl) alcohol solution. Try to avoid touching the belt if
possible - the idea is to keep any grease on the pliers or oil
from your fingers from getting on this belt. |
|
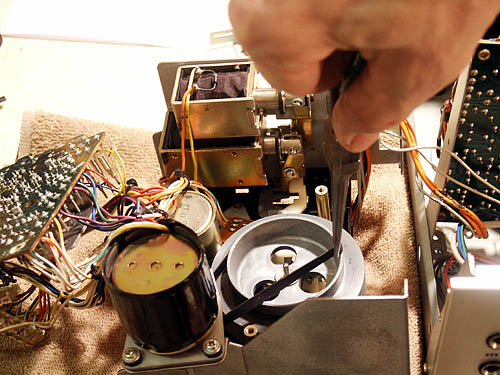 |
|
|
|
Step 23
Next, remove the three Philips screws holding the capstan motor
assembly in place. |
|
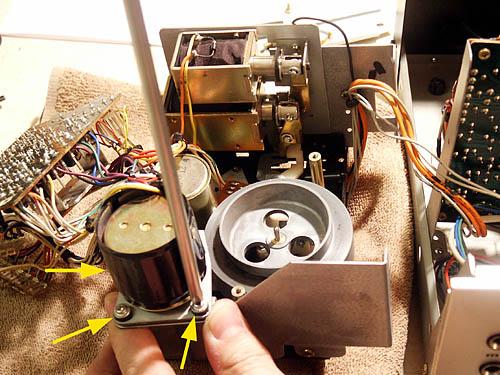 |
|
|
|
Step 24
Lift the capstan motor free of the transport assembly, and set
it to the side. Now would be a good time to clean the
capstan motor pulley with some swabs dipped in your 90% isopropyl. |
|
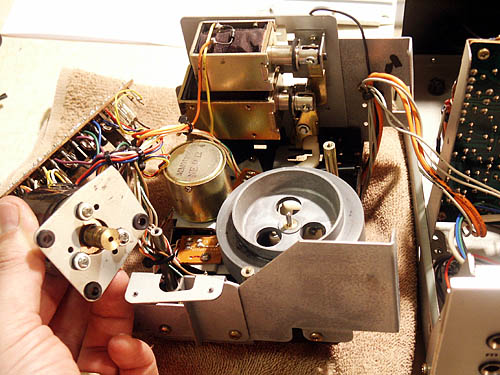 |
|
|
|
Step 25
Pull the flywheel up and out of its bearing, twisting gently
side to side as you exert upward pressure. Notice the belt
residue on this particular flywheel - unless yours is perfectly
clean, use swabs and 90% isopropyl to remove all traces of
residue. |
|
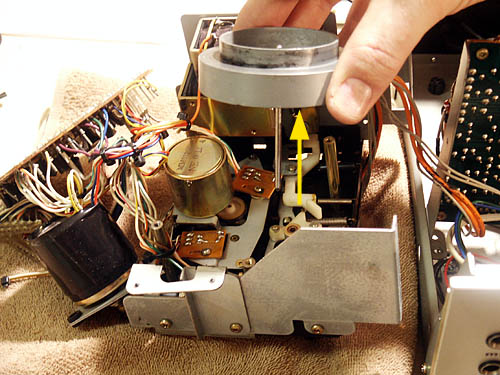 |
|
|
|
Step 26
At last, we have access to the two optocoupler boards (see
yellow arrows). Before you remove the board nearest the
solenoids, scribe a pencil line (see red arrow) along the outer
edge to capture the correct mounting angle to facilitate
reinstallation. |
|
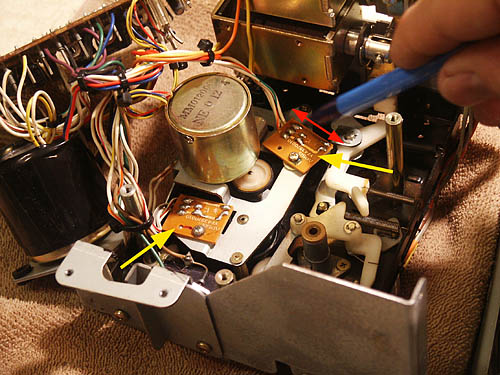 |
|
|
|
Step 27
With your smaller #1 Phillips screwdriver, remove the
optocoupler board nearest the solenoids. There's a washer
underneath this board used to properly space the optocoupler
away from the reel hub. Make sure you don't drop it into
the transport when you
remove the board. |
|
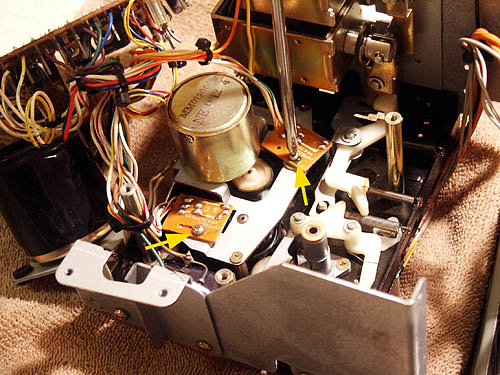 |
|
|
|
Step 28
Remove the second optocoupler board. This one has no
washer below it, and it has a positioning "key", so you don't
need to scribe the mounting angle as on the previous board.
You can see the mounting angle mark for the first board (yellow arrow). |
|
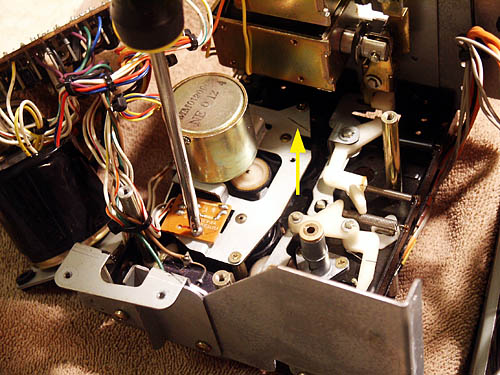 |
|
|
|
Here's the culprit - one of the two defective optocouplers. |
|
 |
|
|
|
Step 29
Desolder the four connections holding each optocoupler to its
board. Solder wick greatly facilitates this process by soaking
up the excess solder. |
|
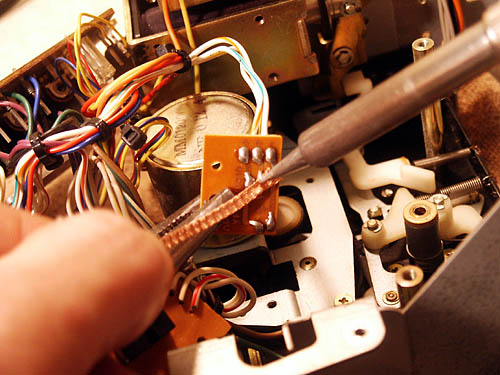 |
|
|
|
Here's a detail
shot of the optocoupler board traces. Note the photo diode
and LED symbols; you'll need to refer to these later when you
install the new components. |
|
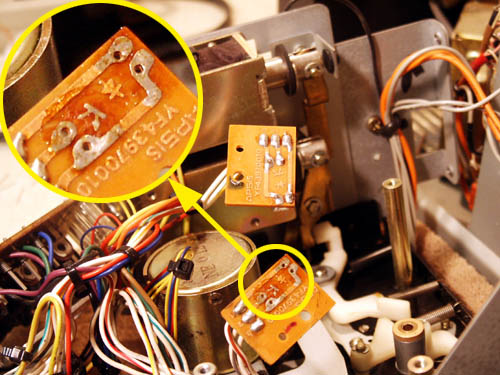 |
|
|
|
Note the size difference between the original parts (at
bottom) and the replacements. Since the replacements are
way too large to be mounted as they are, we'll need to remove the internal
components and mount them separately. |
|
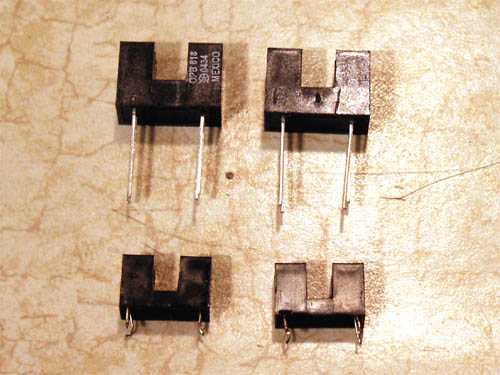 |
|
|
|
Step 30
The trick here is to safely remove the two internal components from their plastic housing without damaging them.
There may be better ways, but here's how I've done it, always successfully,
in the past. With your small #1 flathead screwdriver, gently pry the thin
plastic coating away from the body of the housing until it breaks and you can
remove it, piece by piece. The internal components are housed at the
outer edges of the housing, try to avoid this area as you chip off the outer
plastic. |
|
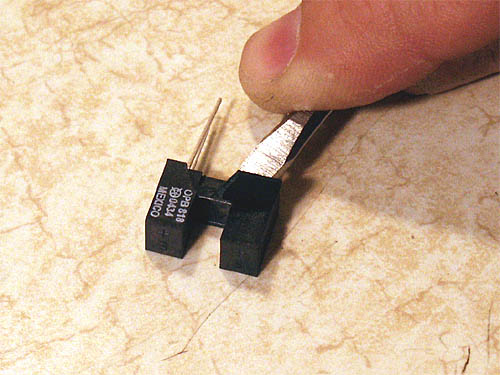 |
|
|
|
Here, we're about halfway done. Notice that the clear infrared (IR) LED is already completely exposed.
Continue removing the outer case until all that remains are the two
components and the internal alignment housing. |
|
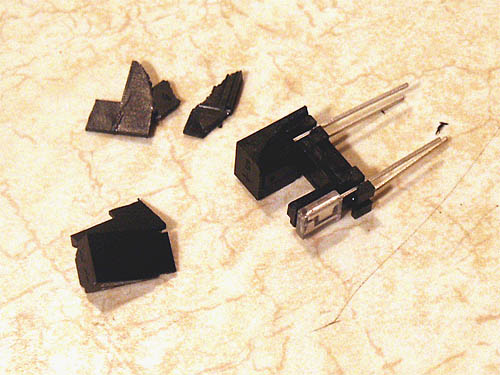 |
|
|
|
Step 31
Here's the new optocoupler with the outer covering completely removed. Slide the two components out of the
alignment housing as shown. |
|
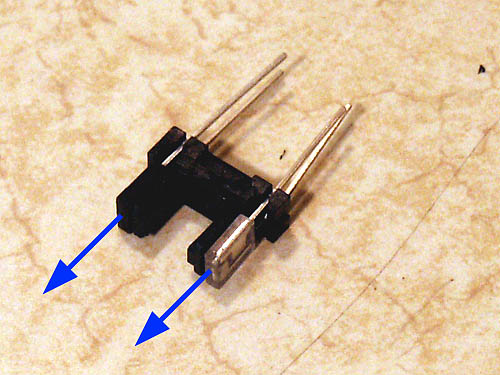 |
|
|
|
The component parts of the new optocoupler
are identified as shown. The alignment housing serves a
dual purpose; that of properly spacing the LED and photo diode, and also
providing a "mask" for the beam transmitted from the LED to the
photo diode.
Without these masks, the beam path would be more susceptible to
interference from outside light sources, and would provide a less accurate switching
pattern. So, while we can't use the alignment housing in our
application, we do need those beam masks... |
|
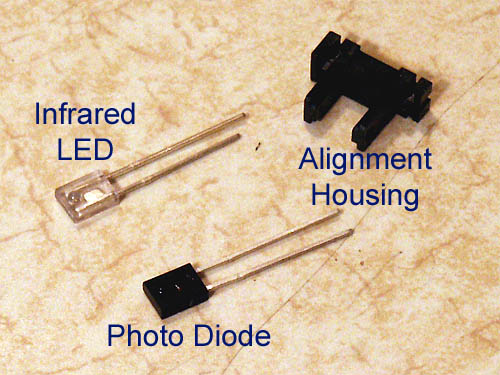 |
|
|
|
Step 32
With your long-nosed pliers, grip one of the beam masks as squarely and as close to the base of the alignment
housing as possible and gently break it squarely off. Repeat for the
other mask. |
|
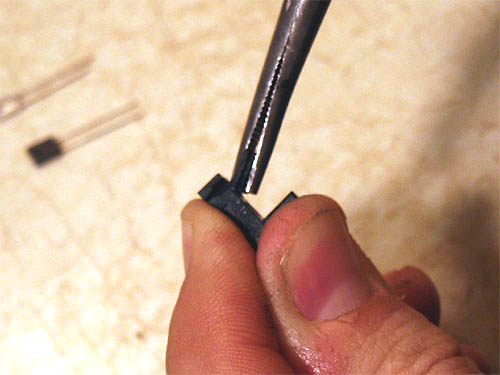 |
|
|
|
Here's a detail shot of the devices with their masks. While it's difficult to see in these pictures, both the clear
LED and the black photo diode have a small bump on one side. Once
installed, these bumps must face each other to complete the light path. The
beam masks, shown next to their respective devices, have a corresponding
indentation to accommodate these bumps so that the masks may mount flush with
the devices. The next step is to attach a beam mask to each device. |
|
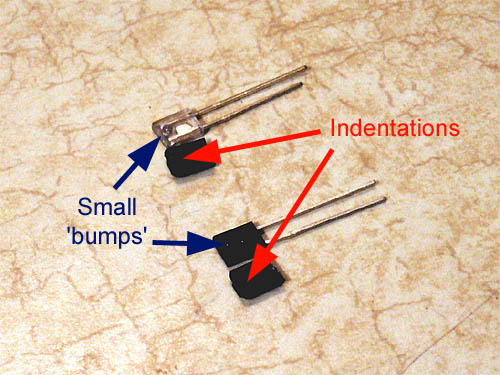 |
|
|
|
Step 33
Place a pin-head sized dab of superglue on the photo diode, just below the 'bump', and apply the beam
mask. Make sure it's square with respect to the diode, and press firmly
together for about 30 seconds until the glue sets. |
|
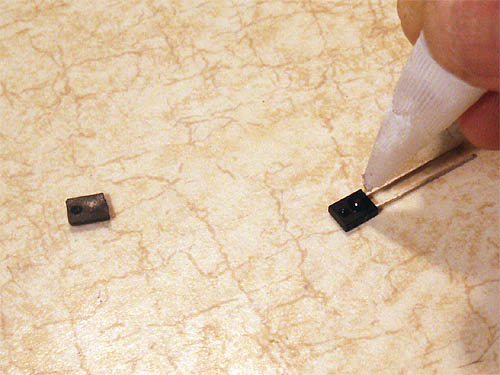 |
|
|
|
Step 34
Repeat step 33 with the infrared LED. |
|
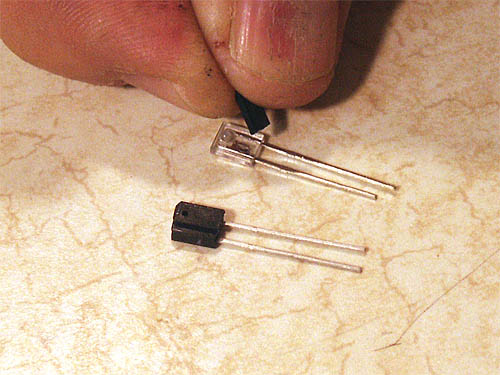 |
|
|
|
Step 35
And, of course, repeat for the second set of optocouplers. The finished
devices are shown. |
|
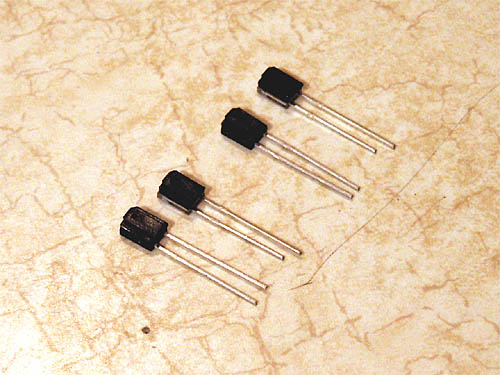 |
|
|
|
Step 36
Mount the first set of devices to the first optocoupler board. Insert leads for one of the IR LEDs (clear
backing) into the holes designated by the
symbol; insert the photo
diode (all black) into the holes next to the
symbol. Ensure
that the holes in the two beam masks are facing each other, then
solder one lead of each device to the
board. |
|
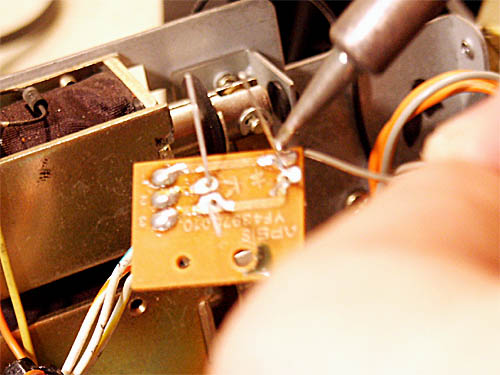 |
|
|
|
Step 37
The purpose of soldering only one lead of each device is to allow you sufficient flexibility to align the two
devices. Use your long-nose pliers to gently adjust both devices so that
they are parallel to each other from an overhead perspective, as shown. This alignment is not absolutely critical, but do the best you
can. |
|
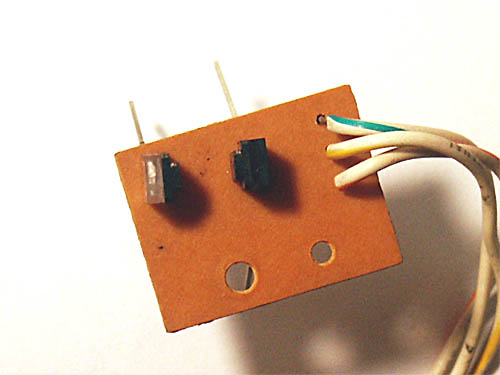 |
|
|
|
Step 38
Now, ensure both devices are perpendicular to the board and thus parallel to each other from a side view.
Once you're satisfied with the alignment, solder the remaining connections
and clip off the excess leads. Repeat for the other set of
optocouplers. It's a good practice to clean excess flux from your solder joints with
some isopropyl alcohol; I find dipping a toothbrush in some,
scrubbing the new joints, and blotting dry with a soft cloth works well. |
|
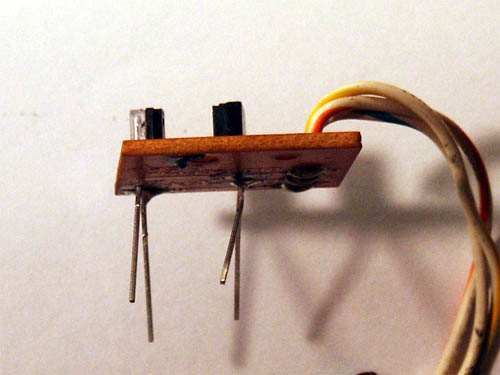 |
|
|
|
Step 39
Remount the optocoupler boards to the transport assembly, being careful to remember the spacer washer for the
board nearest the solenoids. Use your reference mark (from step 26) to
properly align this board before screwing it down. Once both
optocoupler boards are in, spin both reel hubs on the transport to ensure they move
freely, and realign the optocoupler boards as necessary until they clear. |
|
|
|
Step 40
Use this opportunity to thoroughly clean the transport and tape heads, since the transport is easily
accessible. Now is also a great time to install brand new belts and idler tires, so you won't have
to take the deck all apart again in a few years. |
|
|
|
Step 41
Finally, reverse the disassembly steps to reassemble the deck. Fire her up, relax with a nice cold one, and
listen to some old cassettes you haven't heard in a while. Congratulations!
You've resurrected a fine piece of vintage audio equipment - may you
enjoy it for many years to come!
-Dave |
|